Shipping containers are the backbone of international trade and have been since the 18th century. However, while container design and materials have made advancements since then, one thing has remained consistent: the sea. With overseas travel comes the necessity for durability and the ability to withstand all weather conditions. That means there are only certain materials that can be used in building shipping containers.
Each material plays an important role in determining a shipping container’s durability, functionality, and overall suitability for various types of cargo, ensuring it can withstand the demands of transport and storage.
What material are shipping containers made from?
The materials used to construct a shipping container are essential in establishing how they will perform in transit. The two most commonly used materials are steel and aluminium, and each has unique properties, advantages, and scenarios where it excels.
Understanding the differences between these materials and their composition is essential when deciding which type of shipping container you need, as the material will directly influence their performance and lifespan. Understanding a shipping container’s material composition will also enable you to understand its efficiency and environmental impact.
Steel shipping containers
Almost all shipping and storage containers are made using maritime-grade corten steel, especially containers used for heavy cargo shipping. This material is an alloy, which means it’s a combination of steel and other metals. Corten steel is also known as weathering steel due to its durable properties. When a corten steel container is exposed to the elements, a thin layer of oxidisation forms on the outer surface which delivers an additional layer of protection and therefore prevents further rust.
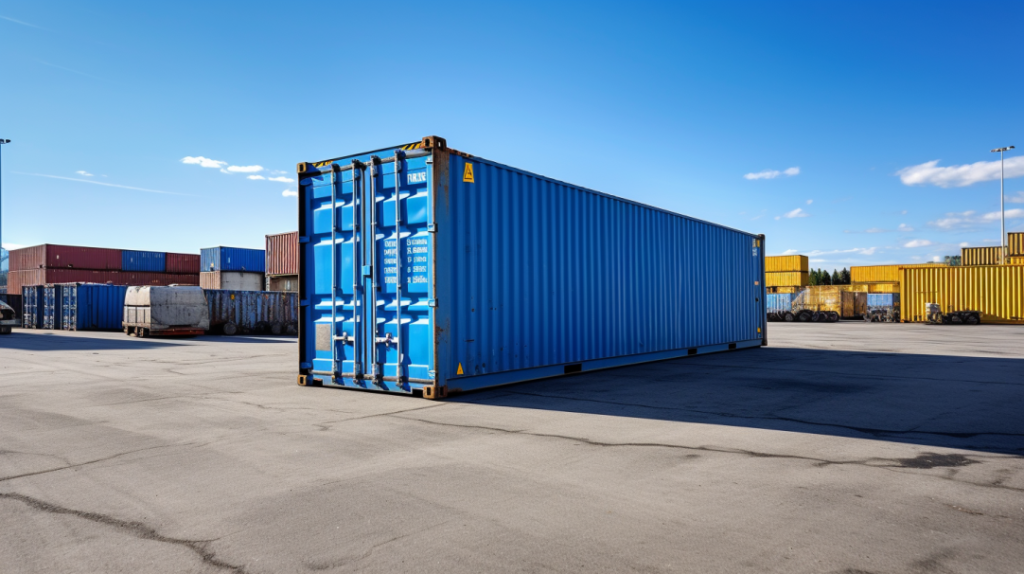
Steel is also extremely weldable which makes it a great option for building shipping containers in different shapes and sizes. This also means it can be used to manufacture other components of a shipping container, including corrugated walls, cargo doors, frames, and cross members. Other properties that add to the appeal of this material for shipping containers include strength, durability, and recyclability.
A key limitation of steel is that it conducts heat and cold quickly, so it can be difficult to regulate the temperature inside. This can be a problem for transporting products that need to be kept at a certain temperature unless modifications are made to the container which will ensure temperature regulation inside the container.
Want to ensure your container stays in peak condition?
Staying proactive with maintenance is key to avoiding costly repairs and extending your container’s life. Learn all about essential upkeep practices, how to spot potential issues, and common repairs to keep your container in top shape.
Check out our comprehensive guide “Expert Advice on Shipping Container Maintenance and Repair” for valuable tips on upkeep and repairs.
Read guideAluminium shipping containers
Aluminium is another popular material for metal storage containers, although it is mostly used for containers that will only be transported domestically and not overseas. This material has many attractive properties including strength, lightweightness, durability, corrosion-resistance, and being 100% recyclable.
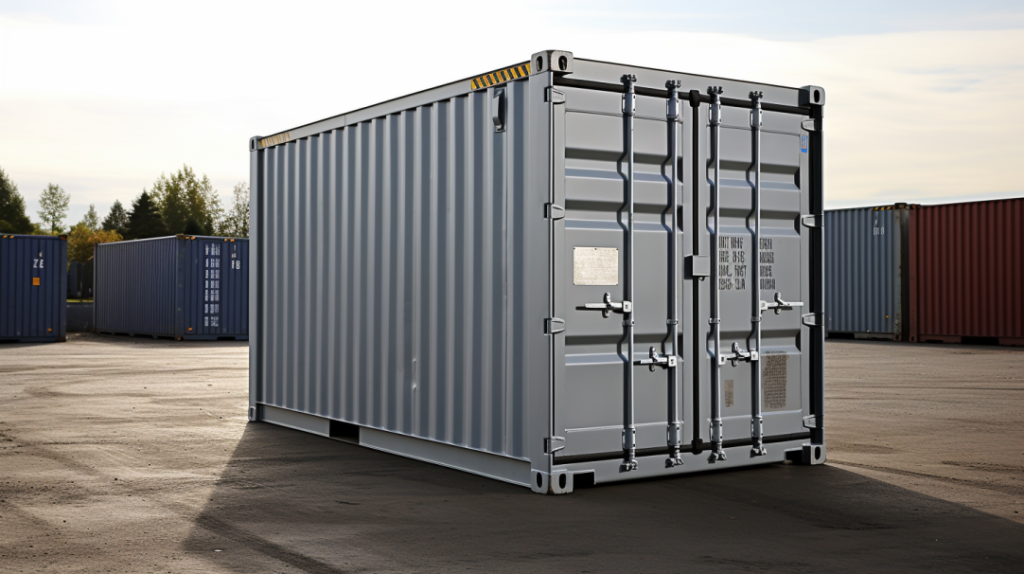
It’s also an economical material for shipping containers as due to its lightweight nature, aluminium offers greater fuel efficiency in transportation. Aluminium containers are also easier to move, transport and load, which decreases the time and cost associated with their use. However, aluminium is often more expensive than steel which can play a role in determining your choice of material.
Aluminium shipping containers are commonly used for products that need to be refrigerated. This is because refrigerated products are generally much lighter than other cargo loads, so there isn’t a need for heavy steel containers to endure the weight of heavier cargo. The weight of the container can be somewhat increased to improve the thermal insulation of aluminium shipping containers when other materials are often installed on the inside of the walls.
One of the main limitations of aluminium shipping containers is that due to their thinner construction, they are not suitable for stacking and creating larger units. Steel containers, on the other hand, are robust enough for stacking.
Polyethylene shipping containers
Shipping containers made from polyethylene are a good option for storing water, hazardous chemicals and other liquid goods. They are manufactured with resins that meet safety standards and specifications that ensure the safe storage of potable water. Polyethylene shipping containers are commonly available in darker colours which reduces light penetration and algae growth.
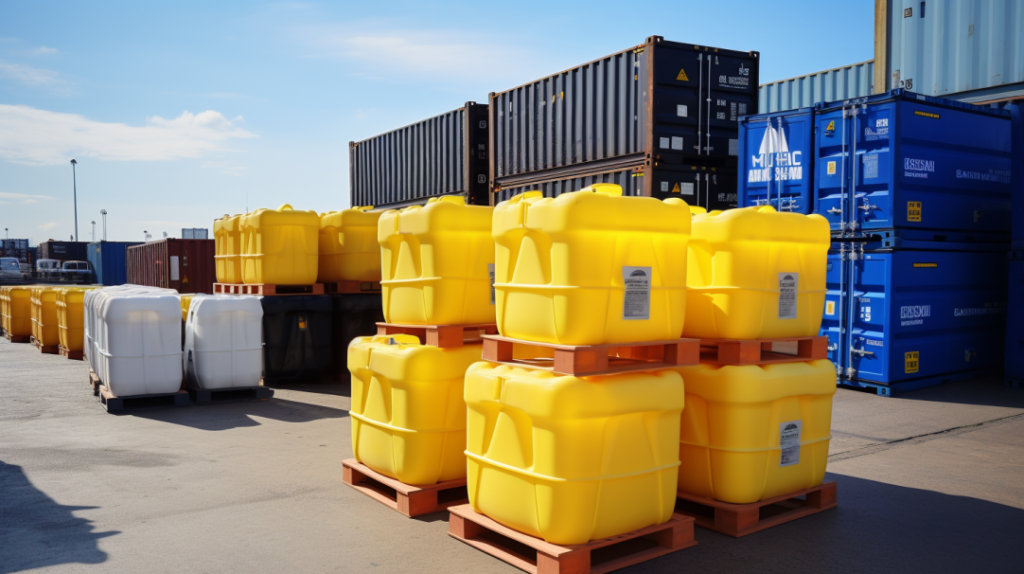
There are two different types of polyethylene used in manufacturing these containers: high-density polyethylene (HDPE) and low-density polyethylene (LDPE). Both materials are highly durable, weldable and chemical-resistant, as well as tough and wear-resistant. LDPE is a transparent, branching variant of polyethylene, while HDPE has a linear structure and is opaque, making HDPE more rigid than LDPE.
Other materials used to make shipping containers
Now that we’ve covered the main materials used to construct the outside of shipping containers, let’s dive into some of the other materials used in the construction of a shipping container. Like the external wall construction, the materials for other elements of a shipping container must be carefully selected to ensure safe and protected transportation of goods.
Flooring materials
The flooring of a shipping container needs to withstand heavy loads and various types of cargo, which means it needs to be made using robust and durable materials. Most shipping containers are constructed using marine-grade plywood flooring, although there has been an increase in the use of bamboo due to lower costs and greater availability.
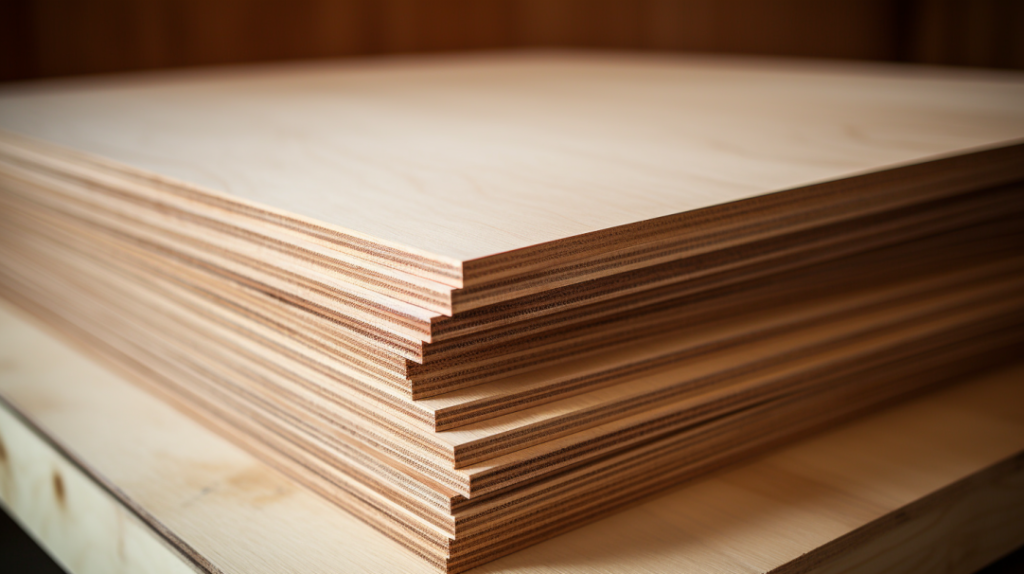
Marine-grade plywood flooring was first created in the 1930s for ship-building during World War Two. It is commonly used because it’s sturdier and higher quality than standard plywood, with much fewer defects that make it longer lasting. Marine-grade plywood is not waterproof, which may come as a surprise. Instead, it is cross-laminated and made with waterproof glue so that when it’s exposed to moisture, it remains intact.
Bamboo flooring has become an alternative as it’s exceptionally dense and hard, making it very durable and long-lasting. It’s also structurally stable, tough and more widely available than marine-grade plywood because it is a fast-growing timber, which also makes it more sustainable.
In some cases, alternative materials like steel, aluminium or composite materials can be used for flooring. This is usually the case when specialised or eco-friendly containers are being built, or different goals or advantages are needed, such as reduced environmental impact.
Paint and coatings
While the materials chosen for the construction of a shipping container are decided based on their durability and functionality, they will also need treatment for optimal protection and longevity. Most shipping containers are exposed to harsh environmental conditions, including saltwater and extreme temperatures, so specialised paints and coatings are needed to help withstand these conditions.
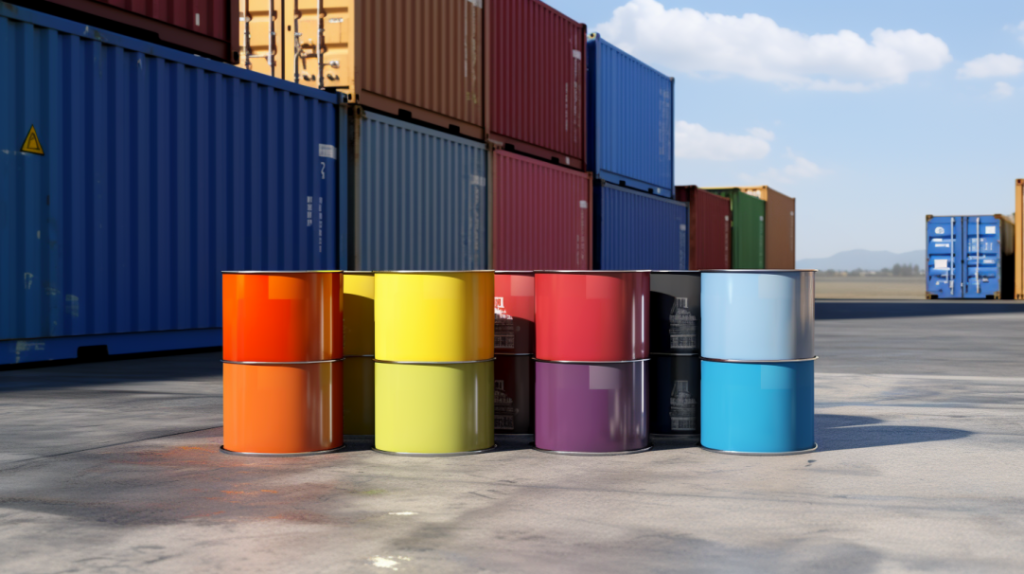
Depending on the requirements of the container, specialised paints and coatings will be used to meet these requirements. For example, epoxy resin is used for its robust water and chemical resistance, polyurethane paint offers optimal UV protection, zinc-rich primers are used for rust prevention, anti-corrosive paints are best for maritime environments, and thermal insulating coatings can regulate internal temperatures.
Specialised paints and coatings each have unique benefits, but all of them serve as a critical barrier in protecting the container from direct contact with corrosive elements and ensuring it maintains its structural integrity.
Looking for paint for you shipping container?
Check out our selection of shipping container paint in any RAL colour you need!
View productsInsulation
With extreme weather conditions likely in transit, insulating a shipping container is important. Maintaining precise temperature control is particularly critical for transporting temperature-sensitive goods, such as refrigerated products. Likewise, if you’re using a shipping container as a living space, you’ll need it to be insulated.
Specialised insulating materials are used for shipping containers, including polyurethane foam, polystyrene foam, fibreglass, vacuum insulation panels, and reflective materials. Each of these materials can minimise heat transfer and maintain consistent internal temperatures.
Components of a shipping container
The materials used to construct the shell of a shipping container are vital in ensuring its structural integrity, but various other components make up a shipping container and each contributes to its functionality. The overall performance and durability of a shipping container are only as good as the materials used in its complete makeup.
From steel walls and frames to locking mechanisms and tight seals, every component should be crafted and designed to offer optimal resilience and efficiency.
Walls and frames
We’ve already gone into depth about the materials typically used for the walls and frames of a shipping container. Steel and aluminium are the main materials used due to their durability and ability to withstand harsh weather conditions, while protecting the goods inside.
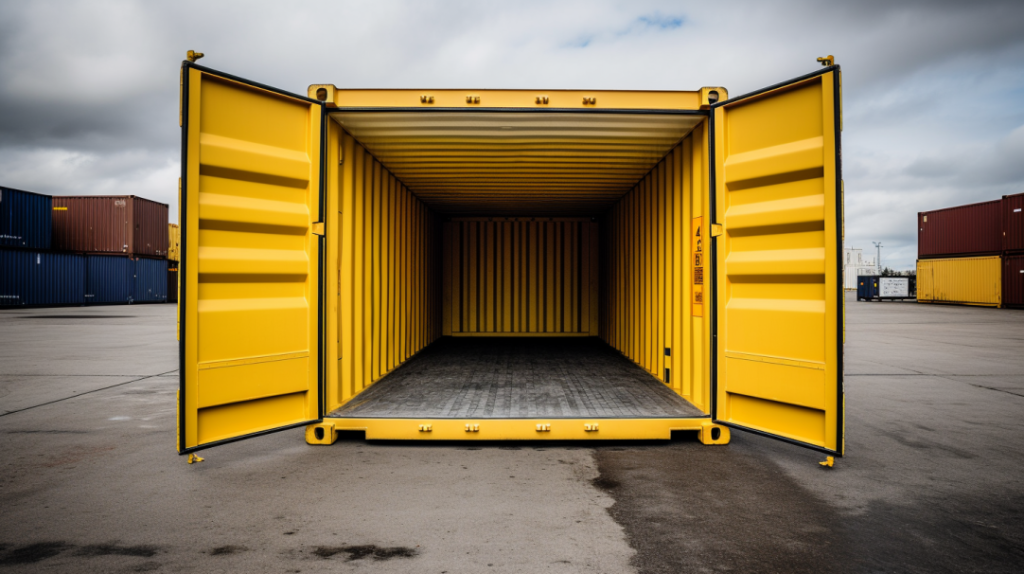
Usually, shipping container walls will consist of 0.075-inch corrugated sheet metal panels welded together. They will also be supported by tubular steel top/bottom side rails and end frames which add further strength to the walls. This strength means that steel shipping containers can typically be stacked as high as nine containers.
Corner castings & corner posts
As many shipping containers are stacked in transportation, they must have robust and reinforced corner castings, also known as corner posts. These corner posts are welded to the I-beams of the floor frame, and when containers are stacked, the corner posts line up to ensure safe stacking.
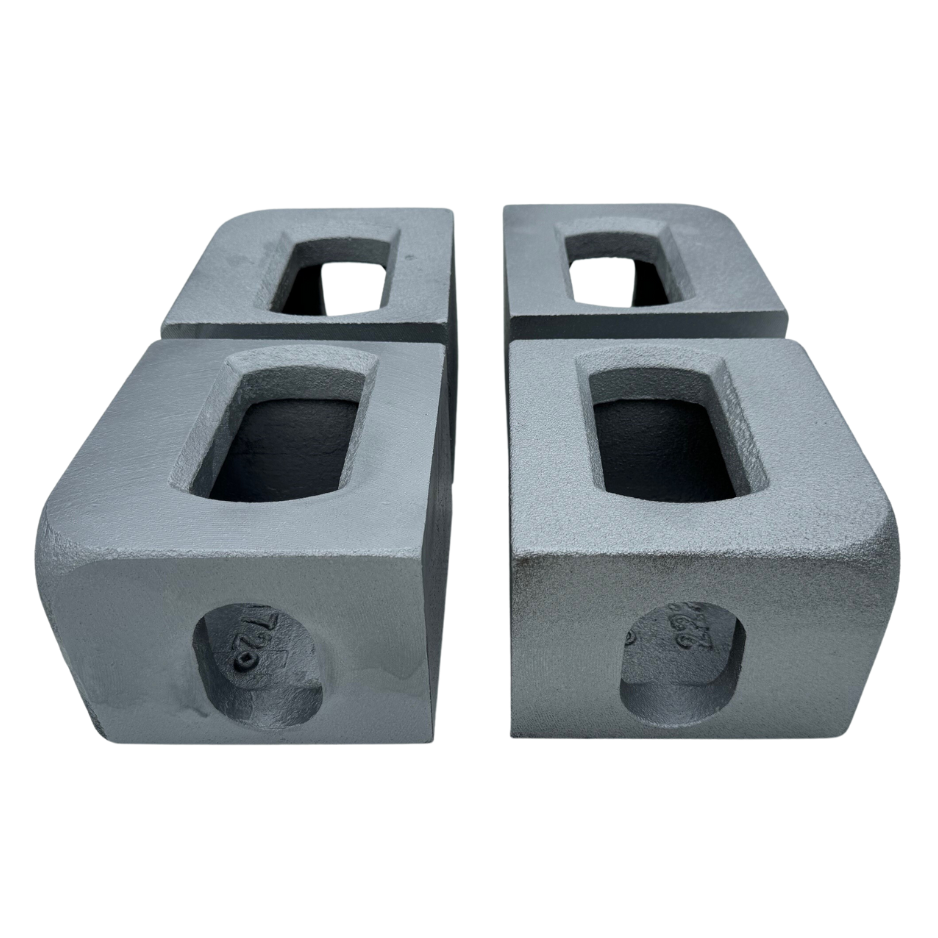
Corner posts are also vital for easy transportation. At each corner post, there are fittings with an opening on the outside. These openings help to lift the containers or secure them onto a vessel, truck, railway wagon, or another container.
Interested in exploring more corner casting options?
Check out our full range of shipping container corner castings!
View productsRoof panels
Like the walls, roof panels are typically constructed from metal, but can also comprise other materials such as fibreglass or composite materials if the container is specialised for temperature control or reduced weight.
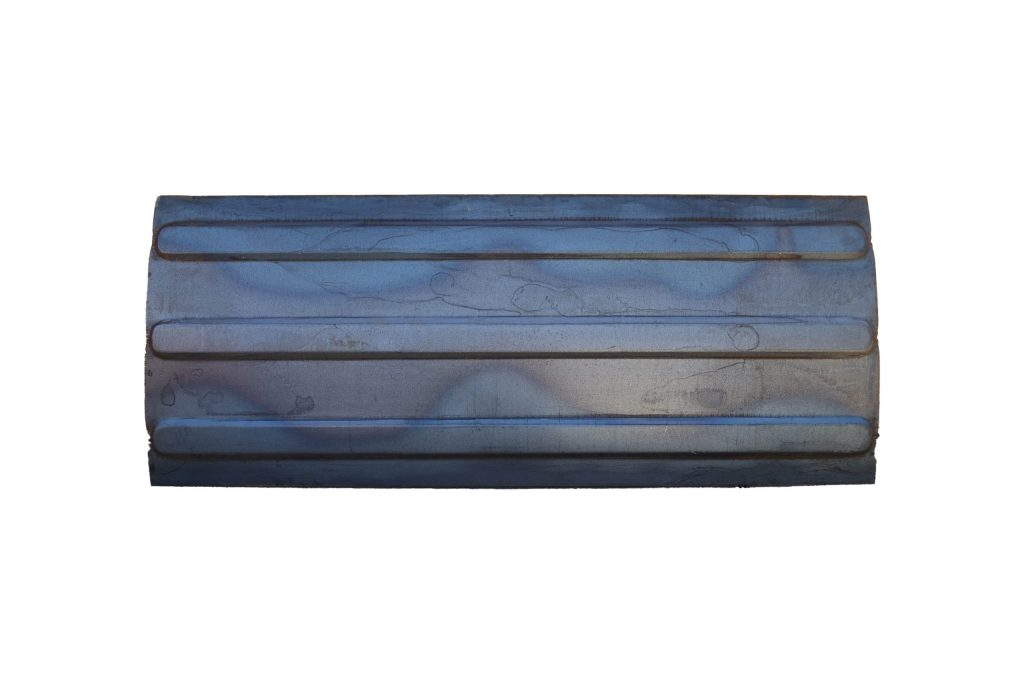
Roof panels fit on top of the shipping container and ensure it is weather-proof. If the container is used for stacking, the roof would be typically made using a stronger material like steel.
Twist locks
As shipping containers will likely come into contact with and need to be connected to other shipping containers, they usually come with a standard connecting system, known as a twist lock.
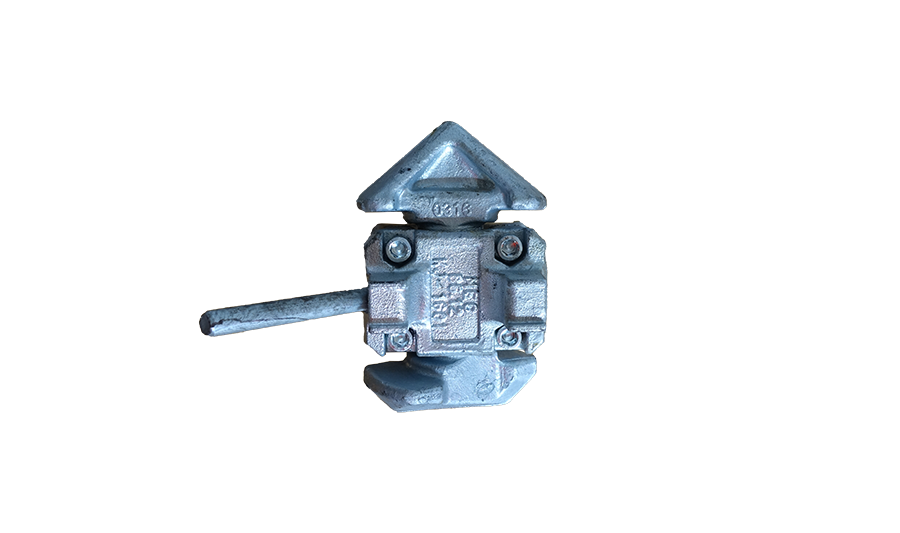
This mechanical locking device is firmly fastened on the corners of a shipping container, enabling it to be securely connected to ships, trucks, container trains and other containers. Twist locks can also help to lift the container by crane.
Looking for locking and securing solutions for your containers?
We offer a variety of twist locks and accessories designed to provide the best locking solutions for your containers. From standard twist locks to locking pins and forged levers, we have everything you need to keep your cargo secure during transit.
Check out our selection of twist locks, stacking pins, forged levers, and more to find the perfect fit for your needs!
View productsCross members
Also known as beams and joists, cross members are structural components designed to lend strength and support shipping container floors by “crossing” from one side to another. They are typically made from steel as they need to be robust and durable to support the rest of the container’s structure.
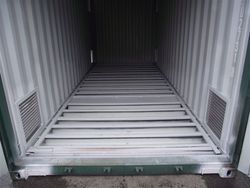
Cross members are visible from the underside of the container and create space between the ground and container floor. This prevents moisture from seeping into the container while also enabling easier lifting from the ground.
Forklift pockets
Moving shipping containers is no easy task, even when they’re empty! That’s why shipping containers include two forklift pockets or slots along their base, enabling forklift prongs to be inserted and used to secure, balance or lift the container safely. These components of a shipping container are a vital design element, providing handlers the ease of stabilising and transporting them efficiently.
Cargo doors, headers, and sills
As integral parts of a shipping container, cargo doors, headers and sills each have a specific role to play in the container’s functionality and structural integrity. Most shipping containers have manoeuvrable cargo doors in the centre of the container, forming two separate doors. They will also comprise several headers and sills. Headers refer to frames at the top of the shipping container, while sills border the other side of the shipping container opening.
Cargo doors
To insert and remove goods from a shipping container, it needs cargo doors. These large doors are often located at one end of the container, although in containers such as tunnel containers or open-side containers, they can be found on both ends or on the side of the container.
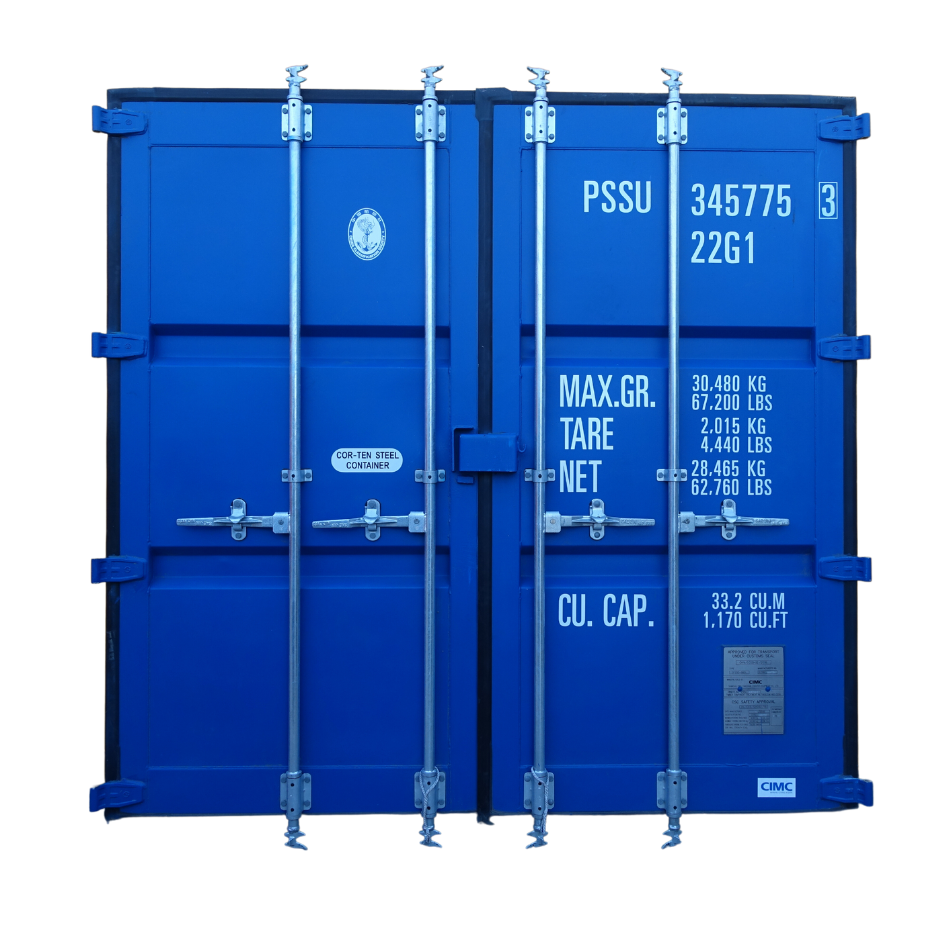
Cargo doors provide secure and wide access for loading and unloading, while also offering robust locking mechanisms to ensure the contents of the container are kept safe and secure from weather, theft and contamination.
Searching for reliable door parts and accessories for your shipping container?
Get all the door parts and accessories you need, from handles to hinges, to keep your shipping container doors functional and secure!
View productsHeaders
A header refers to the horizontal structural beam at the top of the cargo door frame. Headers are essential for adding strength and stability to the container, particularly when the doors are open. They also help to ensure that the container maintains its rigid shape and integrity, supporting its weight and the contents, especially when stacking and lifting.
Sills
A container sill works similarly to the header but is located at the bottom of the cargo door frame. Sills provide a threshold and structural support at the base of the doors, again helping to maintain the container’s shape and structural integrity. They also ensure the doors function as they should, align correctly and seal tightly when closed to prevent anything from entering the container.
CSC plate
One crucial feature of shipping containers is the CSC plate. CSC stands for Container Safety Convention and having this plate shows that the container is safe and structurally sound, and compliant with international safety standards. This standardised system ensures all shipping containers used for international shipping are safe, functional, and meet certain design and construction standards.
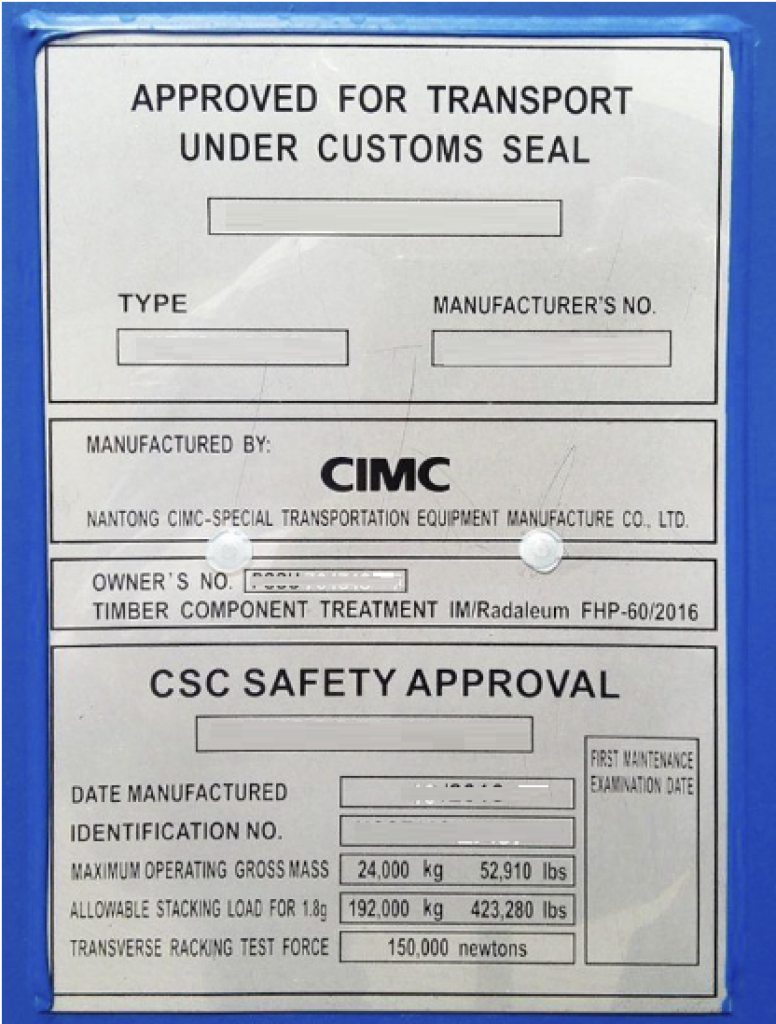
The CSC plate also provides vital information about the shipping container including its identification number, manufacture date, weight capacity, and inspection details, as well as information on structural safety and any tests performed.
Ventilation systems
Shipping container ventilation systems serve several purposes, largely ensuring the safety and preservation of different goods during transit. Containers usually comprise passive ventilation systems such as vent openings or louvres, which are strategically placed to maximise air flow and prevent water from seeping in.
The ventilation system provides vital air circulation which controls moisture and prevents the buildup of condensation which can be damaging to certain types of cargo. Ventilation also plays a role in preventing a buildup of harmful gases or odours and aids in temperature regulation. However, it is not a replacement for refrigerated units. For specialised containers, such as those carrying live animals, advanced active ventilation systems will be used.
How long does it take to make a shipping container?
The length of time it takes to build a shipping container can vary greatly depending on several factors. Typically, it can take around four weeks to manufacture a shipping container. However, it could take longer depending on the specification or any specialised requirements. Some containers can even be manufactured in less time if they are small and straightforward, but it all depends on the specifications.
How are shipping containers made?
Shipping containers are built by combining the various parts and they are typically constructed inside a factory. Manufacturing shipping containers requires a high level of precision and care and involves several steps.
- Fabrication: Shipping containers start with the construction of wall panels, whether using steel, aluminium or another material.
- Tubular steel frame welding: The next step is to create the structural frame by welding a floor frame to support the cargo weight.
- Door assembly: The doors are then added to the container, with corner posts aligned and all parts welded together to ensure strength and water resistance.
- Priming and painting: Once the shell of the container is put together, it is primed and painted for optimal protection against harsh environmental conditions.
- Flooring: When the paint has dried, wooden flooring is fitted on top of the steel floor frame and treated for durability and longevity.
- Decals and identification: Once the main construction has been completed, the containers are branded with company decals and essential identification marks.
- Testing: The last step in the manufacturing of a shipping container is testing. In this stage, the underside is sprayed with a waterproof sealant and the container undergoes load testing to ensure it meets weight capacity standards and is weather-resilient.
Summary
There’s a lot of work that goes into shipping container manufacturing and it all starts with selecting the right materials for the job. Durability, rigidity and weatherproofing are all key features for consideration when choosing shipping container materials.
If you’re looking for your own shipping container, either for storage, international trading or living accommodation, check out our large range of new and used shipping containers.
FAQs
What is Corten Steel?
Corten steel, or COR-TEN steel as a trademark, is a group of steel alloys developed to remove the need for painting and instead, form a stable rust-like appearance after prolonged exposure to the weather. It is commonly used in construction, particularly in the construction of shipping containers. The name is derived from the metal’s two main properties – corrosion resistance and tensile strength.
How thick is the steel on a shipping container?
Steel thickness on a shipping container can vary depending on the component and the structural efficiency needed. However, as standard, walls and roofs are 1.6mm to 2mm thick and doors are 2mm to 2.5mm. The floor frame and cross members use thicker steel to withstand heavy weight, typically between 4mm and 4.5mm. The corner posts use the thickest steel at over 6mm.